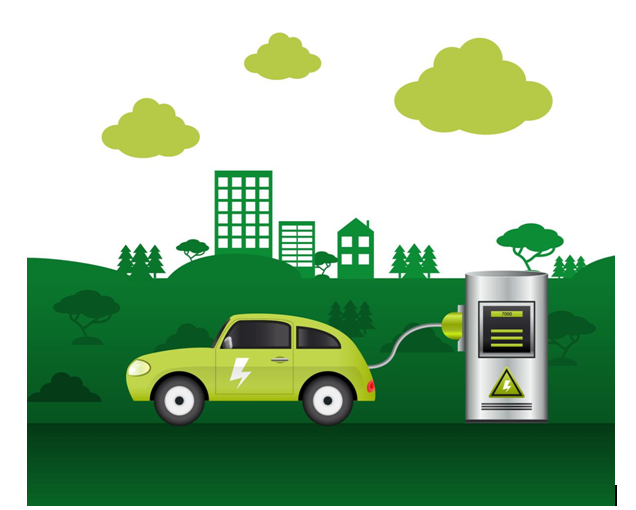
Recent incidents of fires in electric vehicles – two-wheelers ( e-2w) in particular – have brought focus on the safety of electric vehicles. These incidents have put a dent in the growth of EV market, which needs to be urgently addressed.
Causes of fire in EVs
The sources of fire are varied. While most of the fires originate from the battery (thermal runaway), some of the other causes have also been found such as short circuits and glitches in regenerative braking. There are multiple cells in a battery pack, each loading and ageing slightly differently, which may cause what are called ‘hot-spots’ at specific locations in the pack. The charging-discharging cycles can result in abnormally high accumulation of heat at these hot-spots, leading to rising temperatures. However, a battery engineer of a leading e-2W, says that despite the reality of climate change and that summers are getting hotter, an EV battery made up of lithium-ion (Li-ion) cells requires a temperature rise of more than a100 °C before getting into thermal runaway and leading to fires.
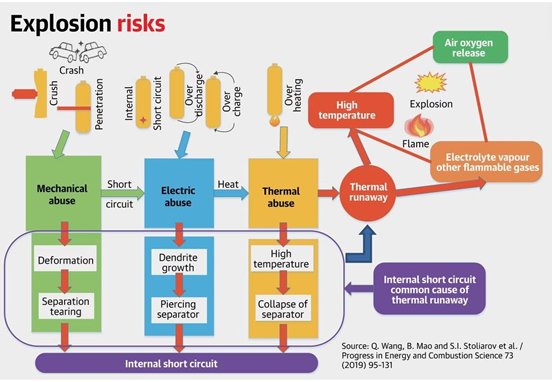
While hot weather conditions and inadequate thermal management systems of the battery can negatively impact performance and shorten life, they do not necessarily cause fires. Manufacturers of most modern Li-ion batteries ensure that they automatically switch off battery operations around 45-55 °C of battery temperature. Even if these safety features aren’t built-in, it’s impossible for the ambient heat and the heat generated by batteries together to result in a spike of over a100 °C.
Preventing fire events with good battery design and protection system
Automotive Industry Standard (AIS) drafted by ARAI address the testing and certification of vehicles and engines used for both automotive and applications. They play an important role in ensuring safer, less polluting, more efficient, and more reliable vehicles.
The standard AIS048 deals with mandatory for battery compliance testing. This was originally used for lead-acid batteries but has been upgraded since for Lithium Ion batteries as well.
There is also a need to have a good battery design to prevent such fire incidents. Cylindrical Lithium-Ion (Li-Ion) cells are a good choice for EVs, which has two internal protective devices: the Positive Temperature Coefficient (PTC) and the Current Interrupt Device (CID) . The PTC protects the cells under external short conditions and the CID protects the cells under overcharge conditions. The casing of the battery should be heat conductive, robust in structure, and have electromagnetic interference (EMI) shielding. The need for effective EMI shielding is especially prevalent in electric vehicles to minimize the associated risks like damage of electrical and electronic components from corrosion, heat, and other challenging conditions.
In the case of an external short circuit, several layers of protection are required such as Battery Management System(BMS) preventive & diagnostic functions, pack fuse, and CID. Batteries also have some sensitive components like MOSFETs, and current resistors that need to be protected. Also, temperature sensors are required to monitor the battery temperatures and alert the user about possible fire risk. Therefore, industry and manufacturers need to spend sufficient time integrating safety features, testing and verifying their products to avoid such accidents in the future.
Regulatory requirements
The Global Technical Regulations are developed under the International Agreement on Vehicle Construction, to which the EU is a Contracting Party. This Agreement currently has 38 Contracting Parties (including the EU, Japan, Russia, Korea, China, India, and the United States of America). The Regulations cover the approval of vehicles’ safety and environmental aspects and are managed by the World Forum for Harmonization of Vehicle Regulations, a permanent working party of the United Nations Economic Commission for Europe (UNECE). In India, The Automotive Industry Standard has over 40 standards published that cover safety from the level of individual components. That testing is concerned with electric vehicle battery safety and lays out requirements of how those batteries must be able to tolerate a wide spectrum of abuse.
Currently, there are AIS156 in-line regulations with AIS136 for the design of electric vehicles and global technical regulations for automobiles and buses. The EVSGTR20 is designed for Phase I of this regulation, which has already been published, and Phase II focuses on electric two-wheelers. Regulations on passenger cars and buses AIS038 (Revision 2) are aligned to EVSGTR20. Regulations have been updated in all other countries in accordance with GTR20.
AIS Standards for Electric Vehicles and Chargers
Standards | Description |
AIS-038 – Electric Power Train Vehicles-Construction and Functional Safety Requirements | It includes requirements of a vehicle with regards to specific requirements for the electric power train and requirements of a vehicle Rechargeable Electrical Energy Storage System concerning its safety. |
AIS-039 – Electric Power Train Vehicles–Measurement of Electrical Energy Consumption | It helps in measuring the consumption of electric energy by electric vehicles |
AIS-040 – Electric Power Train Vehicles – Method of Measuring the Range. | It is a range test for the electric vehicles |
AIS-041 – Electric Power Train Vehicles – Measurement of Net Power and The Maximum 30 Minute Power. | It helps in the measurement of the net power of the electric vehicle and explains the working and benefits of the maximum 30-minute power. |
AIS-049 – Electric Power Train Vehicles – CMVR Type Approval for Electric Power Train Vehicles. | It is a test of grade-ability for electric vehicles. |
As per Deputy Director, ARAI, fire incident is a quality issue against the default because after all, you don’t see every EV battery catching fire, but only a few of them. Therefore, instead of calling on the government to regulate, OEMs need to self-regulate.
India is participating in Phase II of the GTR20, which focuses on heat transfer, water immersion, safety requirements, and more for two-wheeler batteries. For the two-wheeler, the AIS156 was intended for mechanical abuse, thermal abuse, and electrical abuse. Apart from certification and testing, manufacturers need to perform proper design, internal testing, verification beyond certification testing, manufacturing processes, and even pattern recognition charging and discharging.
Ways to extinguish Fire
When the battery is fired, it reaches a temperature of 70°- 90°C. This is shown in various test results. There are many ways to extinguish a fire. There are three ways to put out the fire.
- Lower the temperature
- Separate oxygen from fire
- Remove flammable material
Water cooling is the best method due to its large specific heat capacity (i.e., 4.2kJ/kg°C), it can absorb a significant amount of heat and reduce its temperature. Water also covers the surface of flammable substances, so it can also separate oxygen from the fire.
What can customers do?
- Avoid charging the battery immediately after stopping the EV from running. The lithium-ion cell contained in the battery remains hot for some time. Allow the battery to cool before charging.
- Use only vehicle-specific batteries and charging cables. Using cheaper local batteries can damage your mobility device.
- If the battery is removable, do not place it in direct sunlight or in a hot vehicle. Also, protects the vehicle and battery from extreme temperatures. Batteries and chargers should be stored in a clean, dry, and well-ventilated place. Do not drain or fully charge the battery. Essentially, they should be between 20 – 80%
- Regularly check the battery for damage before use, discontinue use and report to the manufacturer if any are defective. Do not use if the battery is extremely hot or damaged