With the projected demand for Li-ion batteries set to reach 235 gigawatt hours (GWh) by 2030, recycling has become a focal point. This emphasis aims to ensure a sustainable supply of raw materials for cells and decrease reliance on imported resources. Extracting materials through recycling Li-ion batteries is more sustainable than mining. Moreover, the limited availability of key battery materials like lithium, nickel, and cobalt further strengthens the case for recycling.
It was found that recycling has the potential to reduce primary demand compared to total demand in 2040, by approximately 25% for lithium, 35% for cobalt and nickel, and 55% for copper, based on projected demand. This creates an opportunity to significantly reduce the demand for new mining.[1]
Lithium Ion Batteries (LIBs) have multiple components that contain valuable metals and non-metallic materials that can be recovered during recycling. The materials recovered could be used to make new batteries, lowering manufacturing costs. Currently, those materials account for more than half of a battery’s cost. In many cases, batteries—especially in vehicles—are retired from their first use but can be repurposed for secondary use, such as stationary storage. The prices of two common cathode metals, cobalt, and nickel, the most expensive components, have fluctuated substantially in recent years.
Market size: Global vs India
The global battery recycling market is valued at USD 26.9 billion in 2023 and is projected to reach USD 54.3 billion by 2030, growing at 10% CAGR during the forecast period.[2]
“The future of battery recycling looks promising for India Wirth advanced technologies and low-cost processes being developed by the Indian stakeholders. India is and will be setting the examples because India will become a destination for low-cost recycling and refining for the world’s battery rejects or, or end of life batteries.”
- ALN Rao, CEO- Exigo Recycling
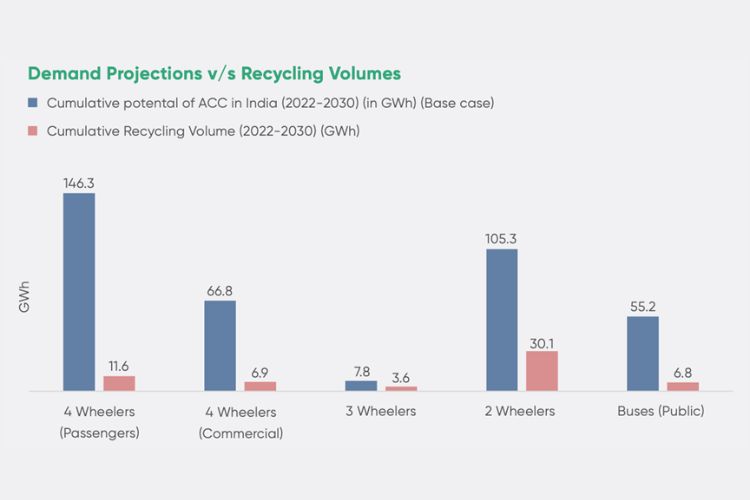
Source: Advanced chemistry cell battery reuse and recycle Market in India, NitiAyog
The figure above illustrates the cumulative demand projections from 2022-30 for lithium-ion batteries in India and the corresponding recycling volumes.
It is estimated that the cumulative potential of lithium-ion batteries in India from 2022-30 across all segments will be around 600 GWh (base case) and the recycling volume coming from the deployment of these batteries will be 128 GWh by 2030. Out of which almost 59 GWh will be from the electric vehicles segment alone.
Components of a Lithium-ion battery that can be recycled
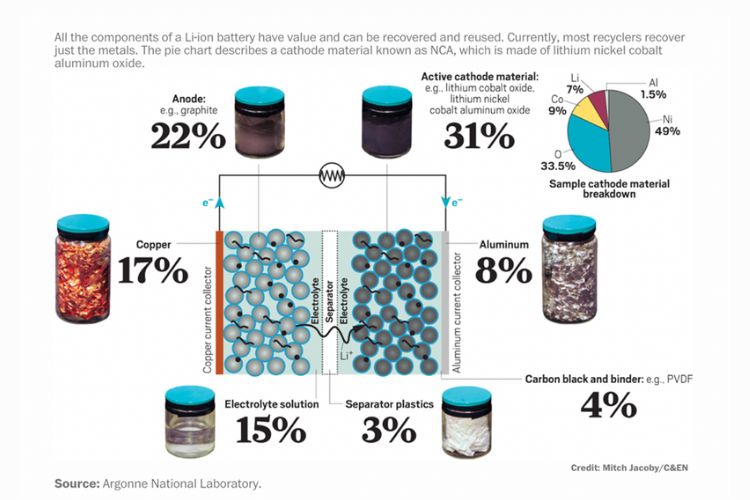
- Ion cells: These are the primary energy storage components of the battery. Recycling involves extracting materials like lithium, cobalt, nickel, and other metals from these cells. During the Preparation stage of recycling, the battery management system (BMS) containing the Li-ion cells is separated from the battery. Through further dismantling stages and treatments, various materials are recovered from the cells.
- Cathode: Typically, the cathode contains materials like lithium cobalt oxide (LiCoO2), lithium manganese oxide (LiMn2O4), lithium iron phosphate (LiFePO4), or other metal oxides. It undergoes various steps during recycling including Washing, Filtering, Pressing and Drying. Consequently, the materials of the cathode can be utilised as active material for new cells.
- Anode: Often made of graphite or other carbon-based materials. Recovering graphite and other materials from the anode is part of the recycling process. Anode scrap that comprises critical materials such as graphite and valuable Cu can be recycled and reintegrated into the battery supply chain. Recovering graphite from anode scraps can provide battery-grade graphite without energy-intensive purification processes and can help support a domestic supply chain. Like the cathode, the anode also undergoes similar steps (Washing, Filtering, Pressing and Drying) during recycling which allow the graphite to be recovered.
- Electrolyte: Generally, the electrolyte is volatile and cannot be recycled. However, in certain frontier technologies for recycling such as Hydrometallurgy, electrolytes can be recycled as well. Recycling electrolytes requires the use of activated carbons which absorb the electrolyte vapours. There may also be the need for an inert gas environment due to the volatile nature of electrolytes.
- Separator: A porous membrane that separates the cathode and anode, typically made of materials like polyethene or polypropylene. Removal of the separator is carried out during the Pre-treatment phase of recycling when the cells of the LIBs are Disassembled. The separator can then be recycled and reused.
- Metal Foils: Thin foils of copper and aluminium are used as current collectors in the anode and cathode, respectively. They are separated from the anode and cathode during the process of Washing. These foils can then be recycled and the extracted Copper and Aluminium are used in the electrical industry.
- Plastic and Metal casings: The outer casing of the battery is often made of plastic and/or metal. Both materials can be recycled. The casing is removed during the Preparation phase of the recycling process itself when the battery is discharged and dismantled.
- Bus Bars and Terminals: These conductive components are used to connect the battery to electronic devices. They are often made of metals like copper or aluminium, which can be recycled. Like plastic and metal casings, the bus bars and terminals are separated during the Discharging and Dismantling (Preparation) phases of recycling.
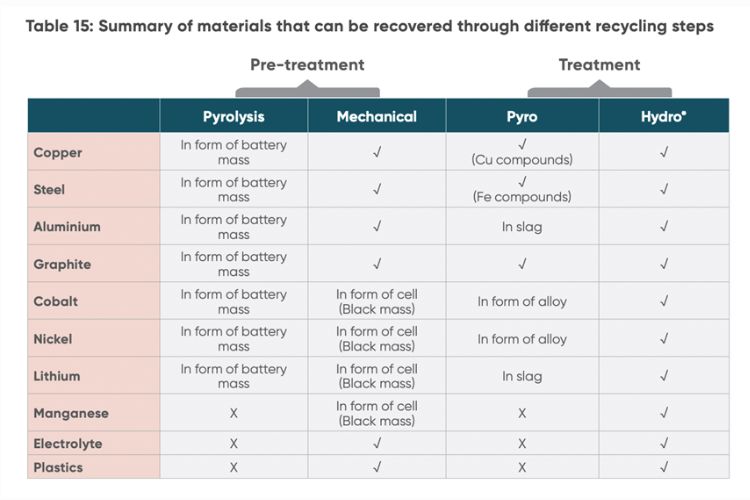
The following chart shows the summary of materials that can be recovered through different recycling processes.
Battery Metal requirements in other industries
Metal | Major Market |
Lithium | Battery manufacturing, glass and ceramic |
Cobalt | Battery superalloys, tools and hard materials |
Nickel | Stainless steel, plating, batteries, Ni and Cu base alloys |
Copper | Building and construction, infrastructure, transport |
Use Cases of Recycled Battery
- Usage in grid-connected solar panels: batteries that undergo damage during transportation and manufacturing cannot be used for their primary purpose i.e., EVs. However, they can be refurbished and recycled to yield battery packs to be used alongside solar panels
- Usage in power banks: Laptop batteries can be repurposed and used for power bank applications.
- Other industrially valuable materials :
- Copper and aluminum extracted from batteries’ busbars find use in the electrical components industry
- Nickel, Cobalt & Manganese are industrially valuable metals finding uses in the electrical, automotive, and housing industries.
- Plastic extracted from the casings of the batteries also finds various industrial applications
More blogs on batteries and recycling-
Why Africa needs to focus on battery recycling
Can Metal-Air Batteries have the potential to revolutionise the automotive industry?